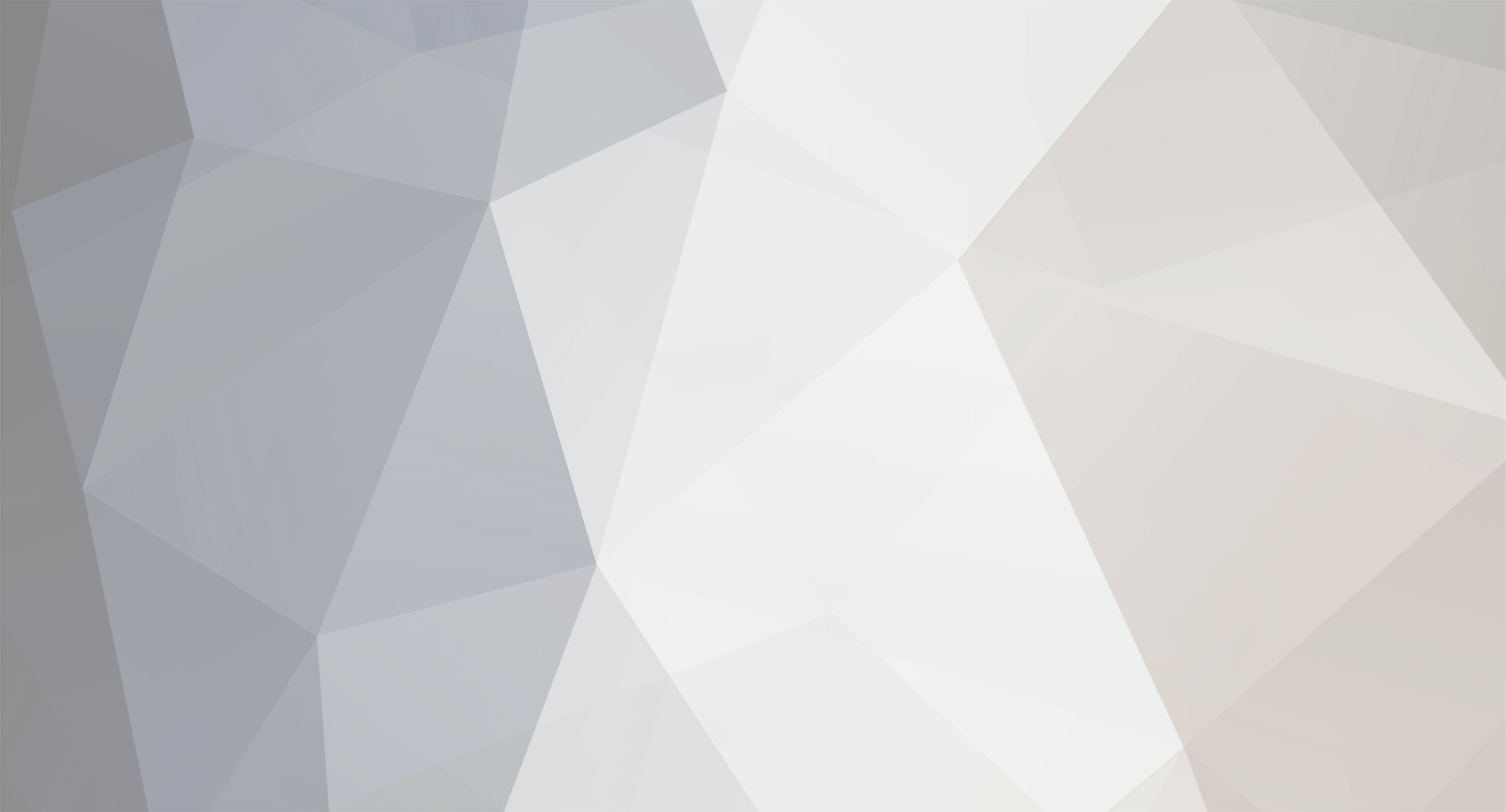
vihro
Members-
Мнения
1026 -
Присъединил/а се
-
Последно посещение
Тип съдържание
Профил
Форуми
Календар
Всичко публикувано от vihro
-
Венелин Венков има специална подписана серия на Алхеми и на мен никак не ми звучат като Стаг.Кольо от бившите Ахед също ползваше за горен чинел на хай-хета си Алхеми.За съжаление не съм ги виждал в БГ, а сега съм в Анталия-тук също няма Алхеми,може би само в Истанбул се намират. http://www.venelin-venkov.hit.bg/barabani.html
-
Аз не бих гласувал доверие на метали правени в Китай-имам неприятен опит с едно супер готино, на външен вид, барабанче на Басикс, чиито натягащи болтове бяха с почти заличена резба,а беше чисто ново.По-евтин вариант от Гибралтар, си остават клампите на Диксън, обаче не съм сигурен тези къде ги правят. Иначе ако разгледаш различните немски сайтове за муз. инструменти,ще видиш,че има и по-евтини ракове от Диксън, включително при Нивелян в София има чисто нов фронт-рак за 250лв.Обаче Драго /Пантомайнд/ ме предупреди,че тея били по-кекави дори от Диксън.Мислех вариант за клампи от скелета,обаче те не пасват на тръбите за рак и трябва да си търсиш тръби от скеле,което пък ще ти утежни целия хардуер.Въобще...получава се един омагьосан кръг.Затова ,закупуването на такова нещо ,според мен, е най-доброто решение. А това което имах предвид за Стаг,а може би и този рак който се продава при Нивелян е, че просто можеш да прецакаш много лесно резбите на болтовете,все пак цялата конструкция трябва да е здраво стегната.А останалото е алуминии,предполагам точно той няма как да се прецака.
-
Това не го знаех-мерси
-
0885 93 29 89,0877 12 22 79 Зоро дърворезбар /София/ Предполагам той може да те светне по въпроса за липата
-
"Шелпак"???? Мисля,че имаш предвид вида на дървото от което са изработени корпусите и последвалата им финишна обработка /от по-евтините модели дори най-висок клас барабани облепени с пластмасови фолиа, различни лакови покрития включително и това което може би споменаваш-ШЕЛЛАК, макар че е прекалено скъп и не съм чувал големите марки да го използват на барабаните си,а също специални масла или графики и къстъм бои, които са най-оскъпяващите скъпите комплекти финиши/ Но като цяло си прав,ако това си имал предвид-дървото и неговата обработка са най-важното нещо което различава скъпите класове барабани от тези в среден и нисък клас Аз си свиря на Ямаха Стейдж къстъм,като в някакъв бъдещ момент смятам да си внеса Келер Мейпъл корпуси и хардуер и да си направя сам барабаните, по същия начин по който си направих барабанчето.Това за мен е най-добрият избор,защото мога да си направя корпуси с параметри каквито аз реша, вместо да залагам на евтин клен като този в Мапексите, които ако не се лъжа се правят в Китай или да разчитам на "големите марки", които обаче са и с ГОЛЕМИ цени ако човек иска да си прави къстъм комплект. В момента ползвам Зилджан К,А къстъм,а серия,разбира се и един средно-тънък райд 20"Аведис.Но смятам да си взема няколко неща от Сабиан Еволюшън като втори сет чинели,само те ми грабват вниманието и слуха в последно време.А готин райд от К или К къстъм Зилджан вече не правят.Така и не можах да си намеря на Дейв Уекъл Зилджан модела.По настоящем модела на Стийв Гад "Сешън" е най-близо до това което беше на Уекъл чинела,но е много скъп.
-
Направо се свържи с "Crow", той имаше такъв рак-мисля сам си го е правил и го продаваше за около 60лв.Ако не го е продал се уреждаш прекрасно,защото изглеждаше много добре.Но така или иначе именно той е човекът който може да ти помогне с повече инфо по въпроса. От мен само следната информация базирана на личния ми рак: Фронталната тръба на рака е 110см.Диаметъра на кръглите тръби е точно 38мм./1.5" се води по каталог/ ,а вътрешния диаметър е 35мм. което значи,че стената на тръбата е 1,5мм. което е важно за олекотяването на цялата конструкция,една от основните цели на рак системата-всичко да е лесно за окачване и да се намали общото тегло на хардуера.А проблема с клампите...наистина нямам идея,може би из магазините за крепежни елементи където има скелета,обаче само за свързване на тръбите на рака под 90 градуса,а за атачването на хардуера на барабаните....нямам идея. Стискам палци за начинанието и ще помагаме с каквото можем Успех.
-
Защо се извиняваш-никого не обиждаш Това ,че твоите омаляват значи само,че имаш неправилна техника и не свириш достатъчно.Но тук има доста информация за различни упражнения и школи,а също как да си изгради човек правилна постановка за свирене на ръцете и краката-потърси по темата.
-
Ако са стари чинелите може с Медикс,а за нови просто трябва да се внимава-Медикса върху памучен парцал и се оставя по-малко време от написаното на опаковката.
-
Май никой не разбра защо инвестираш толкова пари в инструмент първа ръка, щом нямаш професионални амбиции?! Освен разбира се,това което каза Драго за имотите на Витошка А лично за Стаг,в класацията си по качествена изработка на дървените корпуси, ги нареждам дори под прословутите Аматита завладели от време оно нашата мила татковина.Амати на 30 год. ако е добре поддържано,освен малко да са се позахабили носещите ръбове и евентуално леко измятане на окръжността на корпусите,май не се сещам за нещо по-фатално/това,че не вади звук си е съвсем отделен проблем:rocker:/ Докато Стаг още от магазина имат доста по-големи проблеми като разлепени слоеве дървесина, стърчащи парченца дърво отвътре.Дали обаче ще могат да издържат 30год.???? Едва ли. Според мен, последните излезли Тактон са си най-добрият избор /и като изработка и като звук/ за човек свирещ за кеф
-
Има една особеност обаче-изрязването на точен ъгъл за да може от дървените парчета да затвориш окръжност,а не само да ги наредиш едно до друго,както е при паркета.Мислил съм и за тази възможност,но дори теоретически е невъзможно да се получи добър резултат. http://www.snimka.bg/album.php?album_id=170843&photo=42 http://www.snimka.bg/album.php?album_id=170843&photo=43 На снимките се вижда,че е изрязан ъгъл.А идеята на този вид сглобка е по-голяма здравина ако се цели по-тънък корпус. Но все пак ми е любопитно как е решил този проблем Божо п.п. Нормално е масивното дърво да тежи повече,нали затова и звука е по-як
-
Пробвай и ще видиш,че никак не е сложно Само че,ако е само за пробата, работи с по-евтино дърво например чамово.
-
В момента не съм в БГ,като се прибера до 6 месеца ще запиша направо видео. А иначе успех с бонгосите.Самата идея за "stave" барабани идва именно от устройството на бонгосите направени от дърво,само калиброването на струга е по-трудно защото се прави конус.
-
Надявам се есента да се засечем в София
-
Ето линк към снимки на един от сериозните производители на такъв тип барабани: http://hardbopdrums.com/gallery/STAVE-SHELL-DRUMS?page=1
-
Благодаря за хубавите оценки Както и преди съм казвал,не смятам да правя бизнес от това и поради тази причина реших да напиша тюториала,така че всеки да може да си го направи сам.Просто е безсмислено при положение,че все по-малко работа има за барабанисти в БГ,а и тук доста робуваме на марки,така че определено няма пазар за ръчно правени барабани.Същото беше и преди десетина години, когато един ентусиаст като мен, беше направил опит за такъв бизнес,като барабанчетата които правеше бяха наистина много високо качество.Рекламни лица му бяха Владо от Сигнал и Фабрицио от Хазарт,дори Венелин Венков си беше взел такова барабанче и свиреше всяка вечер с него,а тогава беше пика на клубната музика и живите групи.За съжаление този човек фалира,сега мисля,че е още по-зле. А идеята за фолиото е ОК, ако не харесваш шарките на дървото и леко промазания и мек изглед на финиша с масло.На мен обаче, това много ми харесва и дори не съм го ваксал, но пък ако реша може и да го направя по-нататък Но най-важното за мен си остава звука,така че в тази насока определено постигнах желаното,че и отгоре
-
Дано темата да е интересна и полезна http://forum.muzikant.org/index.php?showtopic=37397
-
Моят проект стартира поради една единствена причина-да постигна свое собствено звучене. Идеята ми за 13” основен барабан беше провокирана от по-малките размери барабани и чинели които ползвам в момента, а 8” дълбочина щеше да ми даде по-голяма плътност от стандартните размери. Първият ми избор за материал на корпуса беше плексиглас. Пробвал съм няколко такива модела на американската фирма Ориндж Каунти и ми направи впечатление, че този материал притежава част от топлия звук на клена, а от друга страна яснотата на металните корпуси и по-специално алуминия, който харесвам най-много като материал за малко барабанче. За съжаление се оказа, че в България по-голям диаметър тръби от 20 см. не се продават, а за огъване и лепене на 10мм. плексиглас никой и не искаше да чуе. Затова втората възможност която ми хрумна беше от парчета масивно дърво подредени по принципа на бъчвата. /снимка1/ http://www.snimka.bg/album.php?album_id=170843 Този тип барабани “stave snare drums” са станали доста популярни в държавите с по-развито дървообработване и особено в последните години има тенденция музикантите-дърводелци сами да си произвеждат барабанчета, експериментирайки с вида на дървото и размерите на корпусите. Предимствата на инструмент съставен от масивни парчета дърво пред пластовите модели са: 1. Значително по-малкото количество лепило служещо за свързване на парчетата дърво, което е „мъртъв” материал от акустична гледна точка, т.е. целият корпус вибрира много по-свободно и като единно цяло за разлика от пластовите барабани. 2. В строежа му участва масивно дърво каквото сте избрали, включително скъпи и нетрадиционни за музикални инструменти екзотични дървета, а това дава много нови възможности за избягване от звука на стандартните видове- махагон, дъб, бреза, клен. 3. Възможността да се изкриви такъв корпус е много малка, за разлика от пластовите барабани. 4. Вертикалната ориентация на дървесните влакна подпомага много резонанса на корпуса. 5. Изработката на “stave snare” е в пъти по-лесно осъществима от тази на пластов барабан. Разбира се има и един съществен недостатък-този тип барабани са много капризни и изискват определени грижи, каквито не са необходими за пластовите модели. Резките колебанията в температурата на околната среда, небрежно отношение- силен удар по корпуса или изпускане на барабана могат да доведат до сцепване на дървото. Както и това, че дебелината на стените е по-голяма, за разлика от пластовите барабани с цел здравина, т.е. не са подходящ избор за любителите на тънки корпуси. И все пак плюсовете за мен бяха достатъчни за да се захвана с това. В продължение на повече от половин година събирах сведения за всичко касаещо изработката- от подбора на дървото,лепенето,струговане или фрезоване на корпуса,а след това и фрезоването на носещите ръбове , та чак до видовете финиш.Поставих си още една цел-цялото това начинание да е на професионално ниво,но също така финансово да е около 600лв. каквато е цената за дървените модели среден клас на марковите инструменти. 1.Направа на дървените парчета Свързах се с подходящият човек за изработката на парчетата дърво-единственият лютиер който ми обърна внимание беше Наско /Violins/ и ми препоръча явор селектиран лично от него/снимка 2/. Ето една графика даваща представа за основните данни касаещи направата на корпуси между 10 и 14”/снимка3/ Вижда се,че за всеки корпус трябва да бъде предвиден дори броя на кутийките/машинките,лъгове/ за натягането на обръчите.Основната идея е всеки болт с кутийка да се разполага през едно парче дърво,т.е. парчетата от които е изграден корпуса трябва да са 2 пъти повече от броя на натягащите болтове за една страна-примерно ако солобарабана е с по 8 болта на страна,то парчетата ще са 16,ако е с 10- парчетата са 20.Това е с цел по-лесното оформяне на корпуса впоследствие,а кутийките за болтовете се разполагат по средата на едно парче дърво поради естетически причини,не толкова за да се запази здравината на корпуса ако се пробиват дупките за хардуера в мястото на „шева” между две парчета дърво /доказано е,че корпусите се цепят по дължина на жилките на парчетата дърво,а не на мястото на свързването/На графиката са дадени повечето от нобходимите данни, за да си изготвите парчетата дърво,например дължината на основата на всяко от тях, което има сечение на трапец.За 13” с 8 кутийки на страна /8 лъга/ основата е 2.6087” или 6.62см.Всяко от бедрата на трапеца сключва с правия ъгъл външен ъгъл от 11.25 градуса.Дължината на парчетата зависи от желаната дълбочина на корпуса ,който ще се получи в последствие.Винаги се оставят поне по 20-25 мм. допълнително от двете страни които се отстраняват при струговането-т.е. ако искате барабанчето да е дълбоко 20 см. ,което е 8”, то трябва да направите парчетата дърво с дължина 25см. за да сте спокойни,че ще имате свободен участък,който няма да участва в корпуса на барабана,където да захванете челюстите на струга.Трябва да прецените желаната от вас дебелина на стената за бъдещия барабан,за да определите дебелината на всяко парче дърво.По принцип не се препоръчва да се правят корпуси с дебелина на стената под 10мм.Дори тогава е добре да се използват помощни средства като бисквитки,пръстово свързване,дървени нитове и т.н.Трудното в случая е,че всичко това е свързано с участието на фреза и най-добре направата на бисквитките или свързващи нитовете да стане от същото дърво.Всичко това обаче увеличава количеството лепило в сглобките.За корпуси с дебелина над 15мм. няма необходимост от такива неща и абсолютно съвпадащи и чисти сглобки са най-доброто, което можете да имате.Аз заложих 20мм. дебелина на корпуса,така парчетата дърво бяха с дебелина 30мм. и при струговането имах по 3-4мм. и от двете страни.Идеята е когато сглобите парчетата още преди лепенето,корпуса който сте заложили като данни,трябва да се съдържа във фигурата на многостена /снимка 4 ,макар че съм ги наредил 17 броя а трябва да са 16 но идеята е ясна/.Има още нещо важно което трябва да се знае предварително-корпус с размер 13” всъщност е с размер 12.8750”,14” е 13.8750” и т.н.Така че, като смятате външния диаметър на корпуса си трябва да използвате 12.8750” което е 32.7025 см.И една препоръка от мен-не си правете 13” барабан с 8 лъга /кутийки/ защото ъгъл от 11.25 градуса е ужасно труден за постигане и изрязване,без значение дали ще е на фреза или с електрическите дискови триони за които е необходим електронен прибор за постигане на тези 25 стотни.Затова по-добрият вариант е да се режат 9 градуса което е за корпус с по 10 лъга-такъв хардуер за 13” е почти невъзможно да бъде намерен,а само с 6 става за том , но не и за солобарабан, независимо от предлагането на някои модели.Затова най-лесният вариант е 14” с по 10 лъга на страна.Въпреки трудността Наско/Violins/ се справи с изрязването на 11.25 градуса. Добре е да си направите чертеж,подобен на графиката по-горе с реалните данни,така че да имате сечението на многостена който ще изработвате и съдържащото се в него сечение на корпуса,за да можете да визуализирате всичко,а този чертеж ще е необходим и впоследствие при лепенето. След като сте избрали вида на дървото,изработили сте парчетата които трябва да са по-голям брой от този необходим за конструкцията с цел да се предпазите от възможни грешки допуснати при рязането ,а също така да изберете тези с най-допълващи се шарки на дървото,подреждате селектираните парчета в конструкцията и стягате така че да видите дали има луфтове.Всичко това се извършва на права и гладка повърхност,като използвате чертежа за по-лесното нареждане на парчетата.Ако всичко е наред номерирате парчетата по реда на тяхното подреждане,така че да може да ги подредите отново по същият начин по време на лепенето и да не се губи време.След което следва избора на лепилото, което освен да свърже парчетата и да е достатъчно здраво,така че цялата конструкция да оцелее на струга,но също така до голяма степен би трябвало да запази акустичните характеристики на дъровото и целият корпус да звучи като единно цяло. 2.ЛЕПЕНЕ От предлаганите на пазара лепила Поли Винил Ацетатните са подходящи за целта както и полиуретановите.Трябва да е голяма опаковка 500-700мл. за да не мислите,че лепилото свършва в най-неподходящият момент.Добре е да има отворено време около 30 мин. за да може спокойно да се наредят и стегнат всички парчета. Аз използвах лепило на Бизон „PU Timber MAX Liquid” което обаче не е съвсем подходящо за целта./снимка 5/ Това лепило е поро пълнещо а при положение,че равнините на лепене са съвсем успоредни и гладки,това не е необходимо- вкарва въздух и остават шупли които се разкриват при струговането и се налага да се пълнят отново с лепило.От друга страна лепил съм с всякакви лепила които остават по ръцете ми,например Каноконлит Е се запазва около 4-7 дни,епоксидна смола-около месец,а това лепило след като ми скапа 2 чифта хирургически ръкавици,а отвореното време намаляваше ужасно бързо ,се принудих да лепя с голи ръце-резултата беше,че повече от 2 месеца не можах по никакъв начин да го изчистя от ръцете си,така че преценката си остава за вас.Мисля, че ако отново бих правил барабан, бих пробвал с туткал-достатъчно здрав и има акустични характеристики близки до тези на дървото, за разлика от гореспоменатите лепила.Въпреки това, на запад туткала не е познат, а се лепи със синтетични лепила „Titebond”,”Bison” и др.НО от друга страна, до колкото знам, туткала е водоразтворимо лепило, което на мен не ми харесва,но пък всички лютиери в БГ лепят с него, така че.... Преди самото лепене осигурете си равна повърхност върху която ще наредите дървените трупчета,аз използвах квадрат от ПДЧ.Много помага и чертежа с реалните размери на сечението на конструкцията,за който споменах по-горе.Парчетата дърво се нареждат върху местата си обозначени на чертежа. Ето корпуса залепен/снимка 6 и 7/ Относно стягите- не ползвайте колани като на снимката-разтягат се до някаква степен,но също така остават недостатъчно стегнати участъци по дължината им,а е важно силното стягане.Въпреки тези минуси,голяма част от производителите на “stave drums” използват именно такива колани,НО по-дебели.Малка хитрост е преди да сложите коланите около конструкцията,по-лесно става ако я увиете със стягащо фолио или тиксо,така тя се стяга до някаква степен и е по-лесно да сложите коланите,а от друга страна те започват да приплъзват по повърхността на тиксото и така се изпъват по-добре по дължината си,иначе забират по острите ръбове на дървото.Разположението на коланите е всеки със стягащия механизъм да е в противоположната посока на другия,защото по продължение дължината на колана най-стегнатите участъци са в близост до механизма за натягане,а най-слабите в противоположна посока.Така и от двете страни конструкцията е здраво стегната.Разбира се колкото повече колани, по-добре.Но за мен най-разумният вариант е със стягащи ленти от дебела ламарина които да се стягат на 4 места всяка. Лепилото съхне поне 24 часа,след което сваляте коланите-стяги.Тиксото може да остане-не е проблем защото пада при струговането. 3.Струговане По принцип, подобните на тази конструкция се струговат на стругове за дърво.Монтират се дискове-капаци от дебел МДФ или ПДЧ от двете страни на корпуса,които се захващат с видии на принципа, по който се монтира хардуера /по една видия на всяко второ парче дърво/ Но такива стругове се срещат по-рядко в БГ ,затова всеки струг за метал с големи челюсти ще свърши работа,стига корпусът да е до 400мм. диаметър.Важното е в случая да имате равна основа на корпуса,затова е важно мястото върху което подреждате парчетата по време на тяхното лепене.Ако нямате равна основа много трудно се инсталира конструкцията на струга и е възможно да изкривите мислената ос по която тя ще се върти .Така по дължината си започва да бие настрани и всичко се прецаква. Работих с човек който си разбираше от работата и я свърши перфектно.Добре е да зададете дълбочината на корпуса още на струга,като се пусне по-дълбока стружка,за да имате перфектната повърхност на която ще се режат в последствие носещите ръбове.На тази страна на корпуса която не е хваната за челюстите се прави чело,а на зададеното от вас разстояние от другата страна се прави основата-задавате дълбочината на цилиндъра,но не много дълбоко, така че да не се пререже и да се счупи,а после ще трябва малко рязане, което не е проблем.За съжаление нямам снимки именно от този етап,но не е трудно човек да си представи какво се случва в действителност.Също важно е ,за да спестите от последващата обработка,още докато е на струга да го минете със шкурка до 200. Има още един начин за свалянето на излишното дърво, така че да се получи корпуса и той е с участието на фреза,но поради факта,че има много стругове в България и е евтино,не си струва да се правят специални конструкции над масата на фрезата,а после и фрезата да влезе вътре за да махне дървото и от вътрешната страна-това са излишни главоболия, според мен. След като корпуса е калиброван на струга с точните размери-ако е зададен 13” калибровате на 12.8750” което е 327мм или 14” -13.8750”, задали сте дебелината на корпуса /колкото искате да е дебела стената на бъдещия барабан/,направено е „челото”-т.е. изрязани са онези около 25мм. за които стана дума по-рано,че е добре да ги има и да се изреже такъв ринг за да има права повърхност,същото е направено и от другата страна на цилиндъра, НО не до край и цялата дървена повърхност отвън и отвътре е прешкурена, като НЕ се заоблят ръбовете на челото.Сваляте конструкцията от струга и намирате най-логичния, но и практичен начин да се среже задната част която е била хваната в челюстите на струга на мястото, което е зададено от струга.Става лесно с електрическо трионче с фини зъби, като се водите по среза на струга, а още по-добре на фреза,за която обаче е необходима правилната повърхност на основата и тя да е под прав ъгъл спрямо получения вече цилиндър.След срязването вече имаме готовия цилиндър-корпус за барабана.Срязаното второ чело се заглажда с въртеливи движения на маса на, която има залепена шкурка /другото чело беше изгладено перфектно още при струговането/ 4.Нарязване на носещите ръбове Ред е на най-трудната от всички операции,защото от нея зависи дали барабана ще звучи добре,а именно нарязването на носещите ръбове.Има закон в тази връзка-никога да НЕ се пренарязва един ръб,т.е. не бива още на фрезата да оставяте остър ръб-“apex”.Това води до нараняването му като се опъне кожата,а ако тя е по-тънка/като резонансната на соло барабаните/ може да срежете самата кожа.С няколко думи-прецакали сте всичко до тук!/снимка 8/ Затова винаги се оставя плоска повърхност с ширина 1-2мм която в последствие се взима /заобля/ с шкурка.Това, което трябва да направите първо/не е задължително/,е да залепите една лента хартиено тиксо точно до ръба в двата края на цилиндъра,от вътрешната и външната страна.Това се прави с цел да не се повреди дървото от лагера на носа на фрезера,тогава той се движи по тиксото,а не по голата дървена повърхност.За корпуси с дебелина над 10мм. използвате най-широките ленти тиксо-5 см./Същата процедура е ЗАДЪЛЖИТЕЛНА ако нарязвате или ПРЕнарязвате ръбовете на барабан с вече готов финиш/ При рязането на ръбовете винаги се започва от вътрешната страна!!!Външната има повече декоративна роля от някаква друга,доста често дори не се прави външно изрязване.Добре е да намерите хубава маса за фреза и в случая се ползва фрезер-острие 45 градуса /може да използвате и 60/ Какво острие ви е необходимо зависи изцяло от дебелината на корпуса.Продаваните стандартни 45 градуса вземат до 13мм. т.е. това острие върши работа, ако корпусът е с до такава дебелина.Ако е по-дебел намерете големи фрезери или както направих аз-вкопах малко корпуса с 10мм. около двете основи на цилиндъра. Така се получи идеална повърхност на която мога да режа спокойно с малкия 45 градуса./снимка 9-10/ Нарязвате вътрешната страна и от двете страни на корпуса като внимателно движите с въртеливо движение корпуса по фрезера и вземате по малко,за да не изгаря дървото.Ако решите да режете и отвън оставете около 3мм. ненарязана повърхност върху челото на корпуса-“apex”.Преценете колко е най-малкото вземане на фрезата и направете изрязване от външната страна не повече от 1.5-2мм. и това е в случаите в които нарязвате “snare side” т.е. ръба за резонансната кожа.Трябва да се получи плоска повърхост на челото с ширина 1мм.Така направих аз-на страната за ударната кожа оставих 2мм. широчина на плоския участък-апекса,а на тази за резонансната кожа само 1мм. с което целях максимално да увелича резонанса на тази кожа.За томове и каси 2мм. от двете страни е добра идея , а ако се търси по-голям контакт с дървото на касата може и 3мм. както правят “Reference” серията на Пърл заобляйки изключително много апекса. 5.Изшкуряване на корпуса,изрязване на леглата за пружините и оформяне на носещите ръбовете Ръбовете са изрязани според предназначението което ще изпълняват,ред е на ръчното оформяне на корпуса.Започва се от изшкуряването на външната и вътрешна повърхност преди да се пристъпи към довършването на ръбовете.Поне на мен така ми се струва логично,за да не се рискува с възможното нараняване на готовите ръбове-тук те НЕ са защитени нито от кожи нито от обръчи.Всичко това се извършва на място на което корпуса ще е максимално статичен,идеална работа за мен свърши стойка за клавир.Направете си лапа от парцал който се увива с хартиено тиксо за да остане стегнат и около това „изделие” си завивате използваната шкурка.Така тежестта на ръката се разпределя равномерно по цялата повърхност на шкурене и е по-малко вероятно да вземете на места повече от други.В изшкуряването аз стигнах до шкурка 280 както отвън така и отвътре.Повечето хора търсейки звука на дърото обработват корпуса отвътре с шкурка до 220.Но аз исках по-гладка повърхност. Преди да се завършат ръбовете, специално за солобарабаните се нарязва леглото на пружините./снимка 11/ Това е една екстра, която се въведе като задължителна за всички маркови инструменти в последните години.С това се цели да се намали вибрирането на пружините от останалите барабани,бас и т.н.Представлява изрязване на носещия ръб точно там където минават пружините.Вариациите в дълбочината и дължината на леглата не са големи-дълбочината е ограничена от отвора за пружините на долния обръч.Най-често срещани са дълбочините около 2мм. /повечето модели на Ямаха са с 1.8мм./но могат да достигнат до 3-4мм.Леглата може да са къси, с няколко мм. по-широки от лентата на пружините, или по-дълги до 16-20 см. Моите легла са с дълбочина 2мм. и дължина по ръба 16см.Формата на леглата е различна, но дъговидната и U-образната са най-често срещаните.Най-лесна за машинна изработка е дъговидната с каквато са фабричните модели на водещите марки, а за ръчна е другата.Ето една формула по която можете да си изчислите какво дъговидно легло да си изработите. R= (w2+4h2) / 8h ! ПОЯСНЕНИЕ ! (W на квадрат+4H на квадрат) делено на 8H R - радиуса на окръжността от която ще се вземе дъгата за леглото W - дължина на леглото H - дълбочина на леглото След като сте решили колко да е дължината и дълбочината на леглото,замествате буквите с числа във формулата и се изчислява радиуса на окръжността-например 80см.С конец дълъг 80 см. и молив правите дъга върху бял лист,през която прекарвате права с дължина-дължината на леглото, която сте избрали.В най-горната си точка от дъгата до правата е разстоянието, което сте избрали за дълбочина на леглото.Изрязвате дъгата в пресечения с правата участък и налагате върху външната повърхност на корпуса до ръба,очертавате с молив и дървото се взема с пила или дрелка и шкурка. Разбира се това е по-трудният вариант за ръчна изработка на легло.Лесният е като задатете начална и крайна точка на леглото върху самият корпус и прекарвате шублера с дълбочината която сте задали предварително по ръба.С молив се очертава леглото, което в случая ще е права линия,като едната челюст на шублера се движи по апекса на барабана,а по другата задавате дълбочината на леглото и на 10-15мм. от зададената дължина правите скосявания към точките направени с молив по корпуса.Така се заоблят острите ръбове.Изрязаните повърхности някои оставят равни,други обработват на фрезата с 45 градуса резец,а аз просто си направих ръба на ръка.В случая трябва да имате точна такава, за да работите безпроблемно с пилата.Отново се оставят 1-2мм. плоска повърхност-апекс която се заобля с останалата на ръбовете./снимка 12-13/ Ред е на ръбовете,шкурката е направо 280, за да не се пипат повече.Всяко движение може да е погрешно, затова се внимава и се работи бавно.Няма да обяснявам ролята на ръбовете,мисля за всеки барабанист е ясно,че лош ръб прецаква барабана колкото и да е скъп.Първо се прави по-дебелият горен ръб,защото после ще обърнете барабана на него докато правите тънкия долен-идеята е да не се повреди долният.Необходима е изключително гладка повърхност-стъклена маса върши перфектна работа.Шкурката се държи между показалеца и палеца,като и под двата срещоположни пръста има работна повърхност шкурка и само там. НИКОГА шкурката не бива да докосва ръба отгоре,а само отстрани!!!!Движи се бавно по ръба-стремите се да движите пръстите си по ръба,а не корпуса между пръстите си.Това продължава докато получите хубаво заобляне на ръба-получава се връх/apex/ .Обръщате корпуса и се заемате с ръба на резонансната кожа по цялата му дължина заедно с леглата на пружините. И така корпусът е готов. 6.Финиш с масло От тук следва голямо разнообразие за финишна обработка на дървото-дали ще лакирате за гланцова повърхност, или ще боядисвате /това определено не стои добре на корпуси от масивни парчета където се цели ефекта от шарките на дървото/, или просто ще обработвате с масло, е изцяло ваше решение. Най-лесно е обработването с масло, а и целях матов финиш, затова избрах този вариант.Четящите този раздел са попадали и на темата за Тунговото масло, което така и не успях да си внеса.Затова използвах алтернативни масла за обработка на дърво-маслата на ОСМО и в конкретния случай Топ ойл./снимка 14/ Отделно Ники /Ruidolf/ ми препоръча ленения безир на Леко от който съм много доволен и битката започна.Трябва да спомена,че когато температурите са по-ниски e добре да загрявате маслото, което ползвате на водна баня до 30-40 градуса.Загрявате и корпуса,примерно ако го държите далече от парното,както би трябвало,започвате да го приближавате бавно като оставяте дървото да се адаптира към по-високата температура на въздуха,но и с процедурата по затоплянето на маслото, както и тази на корпуса, не се престаравайте, защото последиците от резките колебания в температурата върху такива корпуси обикновено са драматични. Нанесох първи слой върху довършения корпус с 280 само от горещ ленен безир,с което целях да изкарам шарките,но и маслото да навлезе максимално навътре в порите,защото Топ ойла е по-гъст.Важното в случая е,че „удавих” корпуса в безира-пое доста масло./снимка 15-17/ Оставя се поне 30мин. след което излишното масло се избърсва с кърпа.Почивка едно денонощие.За втори слой разредих Топ ойл с безир в отношение 1:3.Нанасяте отново върху целия корпус и ръбовете,оставяте да поеме маслото, като с всеки слой увеличавах времето за „почивка” на корпуса.След това излишното масло втривате в корпуса с въртеливи движения на пръстите или с цяла ръка,оставяте го още малко и го забърсвате.Отново почивка 24 часа.От третия слой започнах да увеличавам количеството на Топ ойла в сместа и се работи по същия принцип като предходните слоеве,само че не се намаслява вътрешната повърхност на корпуса.Така стигнах до 5ти слой който нанесох само от Топ ойл.Така или иначе дървото не можеше да поеме повече масло. Взема се водна шкурка 1000,1500 и 2000.Започвате да минавате корпуса, НО не с вода,а с масло,за целта използвах от по-гъстите смеси на Топ ойл с безир.Идеята на шкурката е,че хем отваря порите,като отстранява стърчащи частици дърво и така заглажда след себе си,но и втрива масло в новоотворените пори.Оставяте около 1 час-заради безира сместа стяга бавно/само Топ ойл стяга за не повече от 20-30 мин./Можете отново да втриете с пръсти остатъка от маслото, след което забърсвате с кърпа.Понеже не попиваше много масло не беше необходим период на изсъхване повече от 6-7 часа.Така за един ден правех по 4 минавания с един номер водна шкурка,т.е. по 2 минавания на корпуса наведнъж /2 оборота/ Същото нещо се прави и с 1500 и 2000 шкурка,като единствената разлика е,че за 2000 маслото беше доста гъсто, затова използвах по-течния безир.Отново 4 минавания на корпуса.Аз минах и ръбовете и с трите номера шкурка.В края на целия този процес се получава много гладък матов финиш на корпуса,толкова гладък и с топло излъчване,че не смятам да използвам вакси,полирпасти и всякакви други екстри.По принцип трябваше да се мине и със стоманена вълна,НО логиката ми подсказва,че от продаваните на пазара фина и по-едра ,нито една от тях не е подходяща-фината се рони ужасно и с маслото ще стане голямо мазало със стружки,а едрата ще надрасква вече създадения финиш.Положителното на шкурката е,че тънкия филм масло между нея и дървото я поддържа на определено разстояние и така тя взема само ако има стърчащи нишки и не наранява вече създадените гладки повърхности.В крайна сметка се получи лек маслен финиш върху дървото,достатъчно твърд за да знам,че няма да се нарани лесно /снимки 18-24/ 7.Избор и инсталиране на хардуера Важно е да се знае,че хардуера участва не толкова в процеса на звукоизвличане на самият барабан,колкото подпомага или вреди на звученето на барабана.Така изборът му се превръща в голямо предизвикателство за всеки дръм билдър.Аз се спрях на “Super hoops” 2.3мм. ,класическата визия и здравината на “tube lugs” и може би едно от най-важните неща за доброто сътрудничество между барабана с кожите и пружините на резонансната кожа,а имено машинката за тяхното натягане и това тя да работи безупречно и да е с удобен за превключване палец/снимка 25/ На последната малко барабанисти обръщат внимание и тя престава да включва и изключва пружините правилно,което се отразява драматично на цялото звучене на соло барабана. За съжаление на бедния пазар в България професионален хардуер вече не се намира,поради факта,че монополисти като Динакорд не се интересуват да внасят нещо по-малко от...цял комплект примерно,с което предлагането на части за барабани в каталозите се обезсмисля. Какъв хардуер желаете да инсталирате на барабана зависи от това в каква насока желаете да обогатите звукът му.Възможностите за обръчи са много, като всеки тип дава различен привкус на звученето на барабана.Например дървените кленови обръчи, като произвежданите от Ямаха, подчертават топлия звук на дървото, а тези с конструкция на „stave snare” поради по-голямата плътност на масивното дърво ще придадат по-тежко звучене.Алуминиевите обръчи дават по нещо от звука на дървените и на стоманените обръчи ,а 1.6мм стоманени обръчи са малкият събрат на 2.3 милиметровите, които са идеален избор за любителите на “rimshot”-ове. Пружините са другото нещо, което рефлектира на звука и да се направи „правилният” избор е направо невъзможно, защото зависи единствено от вкуса на всеки барабанист-бронзови,месингови,корди като при класическите инструменти, стоманени пружини или съчетанието на корди с пружини, са само част от възможностите в тази насока. Относно лъговете важно е да имат по-малка контактна повърхност с барабана,за да не се пречи на резонанса на корпуса,без да се рискува здравината им разбира се.Останалото е въпрос на харесване дизайна на едни или други лъгове. Инсталирането на хардуера е една нелека задача,направено неточно може да доведе до затруднено въртене на натягащите болтове в лъговете,което е проблем за настройването и добрият звук на барабана .Започва се с определянето местата на лъговете,вентилиращият отвор,машинката за пружините и държача за другия край на пружините,табелката /ако има такава/ върху корпуса,като преди това се залепва хартиено тиксо по дължината на корпуса на местата, на които ще се разполага хардуера.Последното се прави с цел да не се нарани вече направения финиш при пробиването и разбира се да може да се отбележат местата за отворите, които ще се разпробиват. Ако дървените парчета са били изрязани правилно и имате перфектен корпус, т.е. ширината на всяко е като на останалите,определянето местата за хардуера е доста по-лесна задача.Както споменах по-горе лъговете се разполагат в средата на дървените трупчета през едно.За перфектното им позициониране намирате дължината по окръжност на корпуса, като умножите диаметъра по 3.14 /Пи/ Полученото число разделяте на броя лъгове, които ще се инсталират.С това целите да намерите точното им разположение.Примерно за 13” корпус който казахме,че всъщност е 12.8750” което е 32,7см. умножено по 3.14 е 102.678 ,разделяме на 8, защото имам 8 броя лъгове с отвори за болтовете и от двете страни и се получава 12.83см.Значи всеки лъг е на разстояние 128мм. от съседния.Прекарват се прави по дължината на корпуса върху хартиеното тиксо на местата на които ще са лъговете,също се намира средата на дълбочината на корпуса и се отбелязва, като се получават линии перпендикулярни на правите.От тези срединни линии по правите в двете посоки се отбелязват точките, в които ще се инсталират лъговете.Това става като измерите разстоянието между двата отвора за свързващите към корпуса болтове на един лъг.Половината от полученото разстояние отбелязвате от срединната линия в едната посока на корпуса,а другата половина в срещуположната.Това са точките, в които ще се инсталира всеки лъг.Може да се направи проверка дали точките, в които ще се инсталират лъговете са на точните си места по дължината на окръжността.Това става като прекарате един от обръчите през цилиндъра на барабана и там където са ушите, в които ще влязат болтовете за натягането на обръчите засичате с правите, които са прекарани по дължина на цилиндъра, върху които са точките за лъговете.Тези прави с точките е добре да се отнасят към средата на всяко от ушите на обръча.Разбира се възможни са и грешки,особено ако разполагате с по-нискокачествени обръчи,поради тази причина ушите са с леко продълговат профил,а не идеална окръжност. На същият принцип се намират местата и на останалия хардуер.По примера на някои модели на Ямаха, използвах тяхната идея за разполагане на хардуера в зависимост от “Nodal point”,т.е. всички допълнителни отвори /този на вентилиращия отвор,долния отвор на машинката за пружини,както и другата част държаща пружините/ да са на едно ниво с долните отвори на лъговете.Така целия хардуер изглежда по-подреден./снимки 26-28/ Разпробиването на отворите за свързващите хардуера с корпуса болтове започва с изграждането на малка работна площадка, в центъра на която е колонна бормашина или дрелка със статив.Първо трябва да решите дали ще разполагате корпуса върху основата-стиска на статива или ще вкарате стиската вътре в корпуса.Аз избрах втория вариант.Така усилието от разпробиването ще се поема само от пробиваното парче дърво,а не от целия корпус,т.е. всичко е много по-изолирано и се работи по-лесно.За тази цел трябва да позиционирате статива с дрелката във въздуха, за да оперирате свободно с корпуса.Направих си релси от два винкела които в единия си край завинтих стабилно към стругарски метален плот,а на другият им край инсталирах статива с дрелката.В стиската се слага дървена дъска-трупче с примерна дължина 20см и дебелина не повече от 3см.Това се прави с цел вътрешната страна на корпуса да легне върху тази 3сантиметрова страна на дъската, и когато пробивате свредлото да премине от дървото на корпуса в дървото на дъската без да се разперват дървесните нишки.Стиската с дъската се разполага така, че дъската да сочи към вас,така просто нанизвате корпуса на създадената установка,като задължително дъската трябва да е перпендикулярна на вертикалната ос, по която ще се движи дрелката.Добре е всички метални части от направената конструкция, които могат да наранят корпуса да се изолират.По принцип болтовете свързващи лъговете с корпуса са 4мм. а повечето от съвременните лъгове имат къси крачета /около 5мм/, с които навлизат в дървото на корпусите.Тези крачета са с диаметър 6мм.Болшинството отвори за хардуера се разпробиват именно с 2 свредла-4 и 6мм.Прави се тестово разпробиване само на дъската,като свредлото трябва да е насочено точно в средата на дебелината и.Така винаги когато сменяте свредло и променяте местоположението на държача на дрелката върху оста на статива /вдигате или сваляте/,ще знаете къде точно да върнете дрелката, за да стават правилни отворите.След това с 2мм. свредло, с което сте направили тестовото разпробиване се минават всички отвори по корпуса,с което се цели да се взема по-малко дърво, което значи по-точни отвори.След което разпробивате с 3мм. примерно отворите за табелката.Всички останали отвори са с 4мм. свредло като на тези, в които ще влизат крачетата на лъговете правите фаски от външната страна с дълбочина 6-7мм. със свредло 6-6.5мм.Най-трудно е разпробиването на вентилиращия отвор чийто стандарт е 12-13мм.Моят съвет е по възможност този отвор да направите на фреза,защото толкова дебело свредло на дрелката бие встрани и прави отвори с неправилно сечение.Свредлата, които се използват за разпробиването, задължително трябва да не са захабени и с възможно по-къса предна част, т.е. добре е свредлото да е почти плоско отпред за да реже повече от колкото да пробива. Преди да сте приключили правите пробно инсталиране на хардуера като поставяте всичко по местата му и виждате дали пробитите отвори нямат нужда от корекция. Ако всичко е наред от тук нататък има два варианта за това болтовете свързващи хардуера с корпуса да не се развиват лесно-федерки или лепило в резбата на крачетата на лъговете.Добре е да ползвате лепило, което остава гъвкаво след засъхване.Жълтите лепила на Момент които остават като гума след засъхване вършат чудесна работа за тази цел. Инсталирате лъговете,табелката,машинката за пружините и захващача за другия край на пружините,след което събирате барабачето. Препоръчвам да използвате станалите напоследък много популярни сред дръм билдърите,болтове 4мм. с вътрешен шестограм, за захващане на лъговете и машинките за пружини към корпусите.Специално за този тип барабани-„stave” с вертикална ориентация на жилките на дървото,задължително използвате шайби с по-голям диаметър/20мм/ за 4мм. болтове, които свързват хардуера с корпуса.Това е така, защото „tube lugs” са с малък диаметър в контактната си повърхност с корпуса и трябва да се компенсира с по-голям диаметър на шайбите, иначе рискувате при натягане на кожите да сцепите дървото.Задължително смазвате резбата на натягащите обръчите болтове в тази им част, с която влизат в лъговете.Смазвате и механизма на машинката за пружините и след настройката на кожите закачате самите пружини. Има още нещо много важно за този тип барабани и то е,че поради крехкостта на дървените парчета е добре да настройвате двете кожи заедно,т.е. инсталирате бойната кожа като само обирате бръчките,същото правите и с резонансната.След това започвате постепенното натягане на всяка кожа като примерно правите по един оборот на болтовете на горната кожа,проверявате тона на инч от всеки болт, а после правите същото и с резонансната.Продължавате докато настроите барабана според вкуса си. С това работата по барабанчето е приключила. СНИМКИ:29-41 Относно звука на барабанчето-това е един от най-чувствителните дървени корпуси на които съм свирил и то при никакво положение не може да се сравнява с пластов барабан,а единствено с корпуси от масивно дърво- “stave snare” или “segment snare”.Това, че му отнех част от „дървеното” звучене след като минах и вътрешната страна на корпуса с водна шкурка до 1500, ми донесе много по-живо и остро звучене, донякъде наподобяващо звука на един от акрилните корпуси които съм пробвал,с параметри 13х7.5” и дебелина 20мм.Определено достигнах до звук който ме изненада много приятно.Ще направя видео запис като се прибера в БГ, може би след 6 месеца. А ето и колко ми излезе, в парично отношение, цялото това начинание. Цени: 1.Дървен материал /парчета явор/ -130лв + доставка 2.Лепило-25лв. 3.Стяги 2бр.-12 лв. 4.Консумативи/тиксо,ръкавици,ПДЧ плоскост/-4лв. 5.Струговане-15лв. 6.Нарязване ръбове-30лв. 7.Фрезер 45 град.-10лв. 8.Шкурка-3лв. 9.Масла- Ленен безир Леко-5лв.; Топ ойл на ОСМО-34лв. 10.Хардуер-332лв+ доставка 11.Консумативи /Евроболт/-12лв. ОБЩО: 612 лв. За сведение YAMAHA Musashi 13x6.5”-335 Евро /по цена на Динакорд/ КОНТАКТИ: Наско /Violins/ лютиер- atanasandreev27@ mail.bg Телефони давам на ЛС: ПРЕПОРЪЧВАМ ГО! Тодор Йорданов /стругар/ Надежда 2,ул.Свети Климент 38,тел.02/936 17 69,0888 83 75 89 synthese@abv.bg Зоро /фреза/ нарязване на ръбове- zmey@mail.orbitel.bg 0885 93 29 89,0877 12 22 79 Той и колегата му вече знаят, за какво става въпрос,но не разполагат с хубава маса за фрезата както и резец 45 градуса/купих си го/.Освен това при фрезоването вземат наведнъж дървото,а не на порции и то изгаря на места,така че вие си преценете. Масла ОСМО –ул. Виктор Григорович 32 /Магазина се намира срещу арката на Александровска болница/ office@phivex.com Хардуер- Гарет http://www.highwooddrums.co.uk/ а дребните неща са от: Евроболт /крепежни елементи/ ул.Раковски 26 ,02/931 81 21 Там ще откриете огромно разнообразие от всичко свързано с ремонта по хардуера на барабаните-болтове с вътрешен шестограм най-различни дължини,шайби и др. !!!Огромно количество информация относно всичко свързано с ремонт и изработка на барабани,можете да намерите в следната страница: http://forum.drumshed.org/index.php Успех на всички ентусиасти в изработката на барабани.
-
Готов съм напълно и до 1-2 дни пускам тюториала с много снимки.Дано повече хора да опитат алтернативните на тунга масла
-
Търси се каса като на John Bonham за Molotov!
topic отговори на vihro's metalhammer в Ударни инструменти
Но не и акустични,ако питаш мен.Другият негатив е,че е крехка - като си инсталнеш лъговете и започнеш да натягаш болтовете за обръчите ще се счупи.Разбира се до това не може да се стигне,защото ще се строши още щом се опиташ да направиш носещите ръбове на фреза. Хората са открили,че корпуси за барабани могат да се правят само от следните изкуствени материали: 1.Акрилно стъкло/плексиглас/ 2.Стъклопласти/фиберглас/ 3.Графитни влакна 4.Разбира се и различните видове метали-алуминий,месинг,бронз,стомана,мед,титан. Мислил съм и за текстолит,някой ден може и да пробвам -
При положение,че инструмента е от дърво,СПОРЕД МЕН,никакви сериозни температурни манипулации не са добра идея,нито в посока висока температура,нито ниска.И при двете крайности има сериозна опасност дървото да се спука. На едни стари барабани съм пробвал с каноконлит и резултата беше много добър,нищо не се появи повече.Но така разваляш акустиката на дървото,защото това лепило е с висока порьозност и заема голям обем дървесни пори .Възможно е същата работа да свърши обикновен безир,като така отравяш средата на живот и смятам,че ще измрат.Най-добре е лютиерите да кажат,иначе само ще предполагаме какво може да се направи.
-
Търси се каса като на John Bonham за Molotov!
topic отговори на vihro's metalhammer в Ударни инструменти
Плексигласа е фешън,но НЯМА акустичните характеристики на дървото,въпреки твърденията в по-горен пост.За барабанчета, също и бонгоси е супер /разбира се зависи какъв звук търсиш/ , но за останалите барабани в комплекта не е добра идея.Иначе всеки в студио щеше да записва с плексигласови корпуси. А за направата на барабани от плексиглас повече от 8" в БГ е невъзможно,поради 2 причини: 1.По-големи тръби от 20 см. в диаметър не се продават. 2.За лепене на плексиглас никоя фирма работеща с този материал не иска и да чуе.Това значи,че трябва да си оформяте корпусите като извивате плексиглас на ръка използвайки пистолет с горещ въздух,а изработването на матрица с точния "under size" е ужасно трудно.Но все пак може да попитате Пепи Славов,мисля че е единственият човек който някога е правил това и резултата не е бил много добър.Той беше човекът отказал ме да си правя барабанче от плексиглас като го лепя. Скоро в раздела за изработка и ремонти на музикални инструменти,ще постна тема-туториал как да си направим барабан от масивно дърво. -
Днес получих хардуера,утре инсталирам и скоро пускам туториала с доста снимки
-
Не се прецаквайте да си вземате HQ,АКО са по-скъпи от тези на Про марк.Аз се прекарах да се подведа по надписа "real feel"/от малоумие най-вероятно/ без да пробвам Про марк,защото когато съм го купувал в Корея цената на HQ-то беше по-висока.Качеството на изработката и усещането за мен, беше абсолютно едно и също-и двата са един и същи "feel",че не е "real" то е ясно
-
След като не ви харесва темата защо продължавате да коментирате?! На мен пък ми харесва идеята да понаучим малко повече за нещата около свиренето на БГ барабанистите лично от тях,а не само да ги оплюваме и без това подфорума за барабани като цяло заприлича на кошче за боклук и от месеци не съм виждал някой да постне интересна тема.Разгледайте някой чужд музикантски форум и вижте дали там се излива такава помия като в този раздел????
-
Чакам си хардуера от Англия и написах туториала до тук,като инсталирам железата ще постна новата тема.Ако искаш ще ти пратя снимки да видиш финиша с двете масла Сори за офтопика.